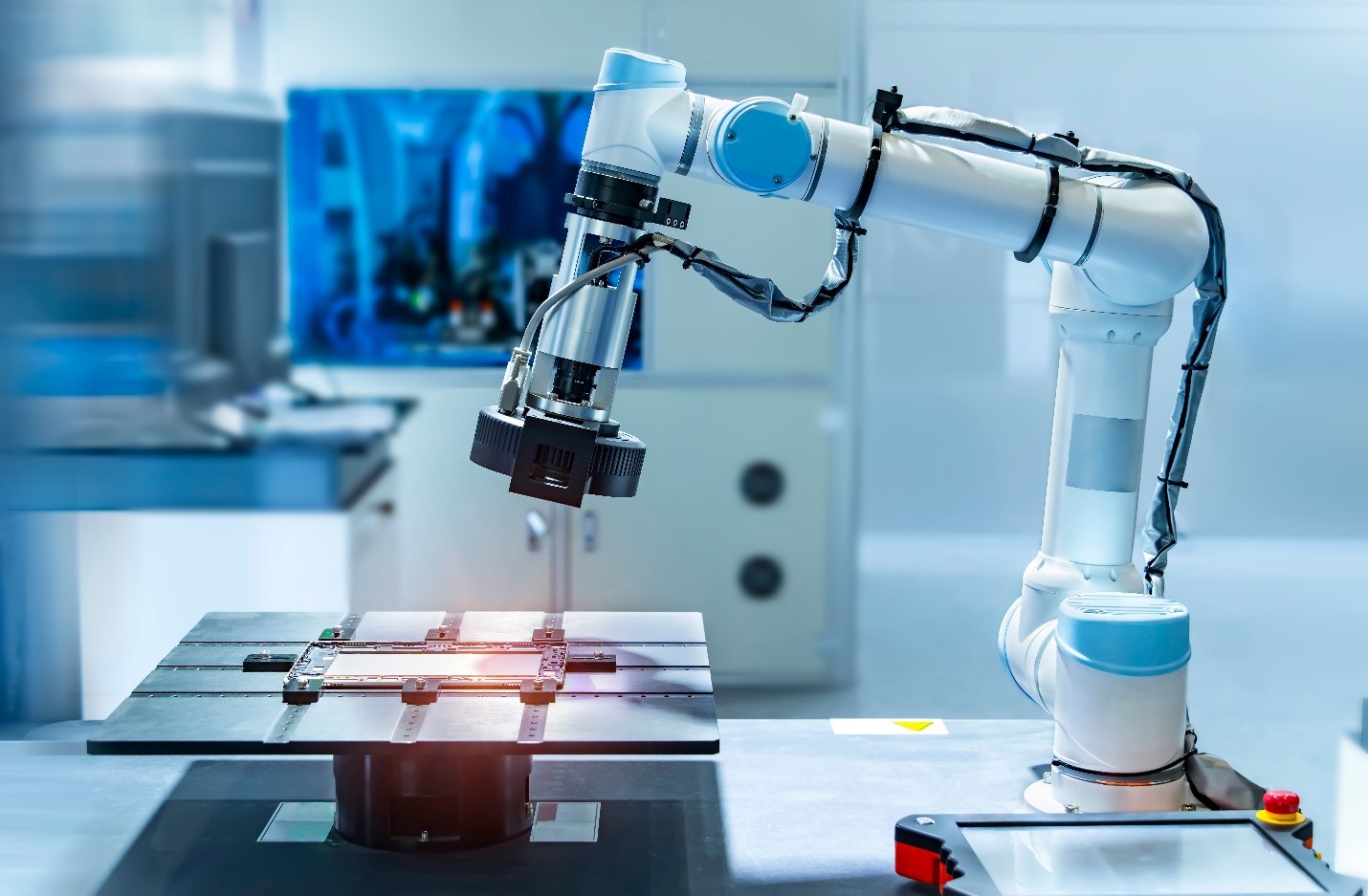
Examples of applications for industrial collaborative robots (Cobots)
Collaborative robots, or cobots, are revolutionizing the industrial landscape. Designed to work alongside human workers, these robots enhance productivity and can help address labor shortages. Their capabilities will make them essential in many sectors, including assembly, packaging, quality control, and more. Explore some applications and see how they can be integrated into your work environments.
Assembly
Cobots are used for assembly tasks that require repetition or precision. For example, in the electronics industry, they can assemble delicate components without the risk of damage.
Box forming
Cobots are ideal for handling and packaging tasks. They can form boxes.
Case packing
A cobot can replace the operator at the end of the line to pick up boxes, bottles, bags, or other items and place them in crates.
Inspection and quality control
Combined with cameras, collaborative robots can perform visual inspections and quality checks. They can detect defects, take measurements, or validate assemblies, ensuring consistent quality for each product.
Handling
If you need to move parts between two lines, on conveyors, transfer them from one piece of equipment to another, from a feeder tray to a machine, or from a machine to a bin—why not add a robot?
Palletizing
Cobots are ideal for palletizing boxes. They can lift and move heavy objects with load capacities of up to 30 kg, thereby reducing the risk of injuries for workers. Various accessories are available to enhance gripping and extend the reach of the cobot.
Polishing or sanding
Need to sand or polish parts? Cobots can apply consistent force throughout entire days without getting tired. They are designed to work in dusty environments.
Welding
In metallurgical industries, cobots are used for welding tasks. Their precision and ability to operate in safety mode ensure high-quality welds. It is also easy and quick to adapt the programming according to the products.
Machining
Feeding machining centers or machine tools is a good example of application. It prevents an operator from waiting long minutes for the end of a machining operation. It also allows for extended work shifts.
Screwing
Cobots can perform screwing operations, even with small screws, with great precision. It’s easy to quickly reprogram the robot to adapt the screwing process to different products. Industrial cobots are versatile and can enhance the efficiency and productivity of various operations in the manufacturing sector, including for small and medium-sized enterprises (SMEs).
Do you have an application idea?
RES supports you throughout your project, from analyzing your needs to implementation, including training your teams. Do you have an application idea? Don’t wait, contact us to meet with one of our professionals and explore the possibilities that cobots can offer your business.