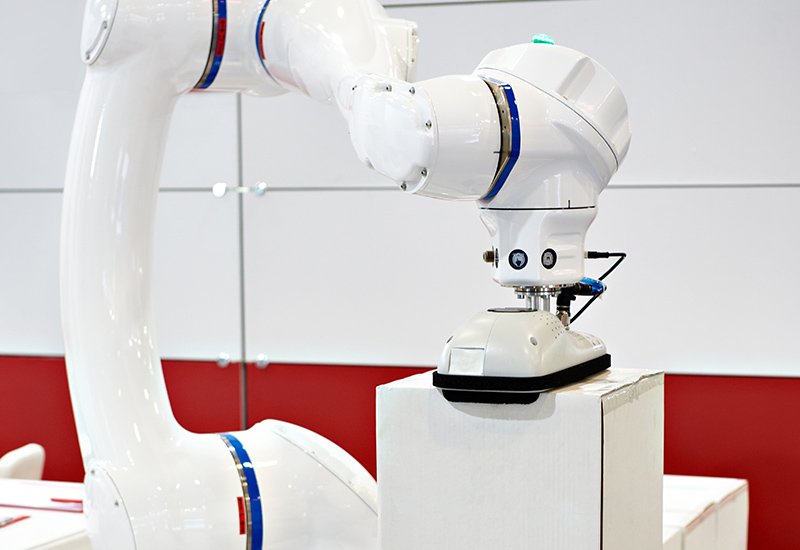
The new safety requirements for robotic systems
Technologies are constantly evolving, and standards must adapt to ensure a safe environment for workers. ISO-10218-2, which covers safety requirements for robotic systems and integration environments, was revised in 2025 to incorporate the latest technological advances and strengthen the safety of collaborative robots. These changes aim to align safety practices with technological advances and facilitate the integration of robots into modern industrial environments. Here’s an overview of the main new features. Main new features of the ISO-10218-2 2025 …
Read More
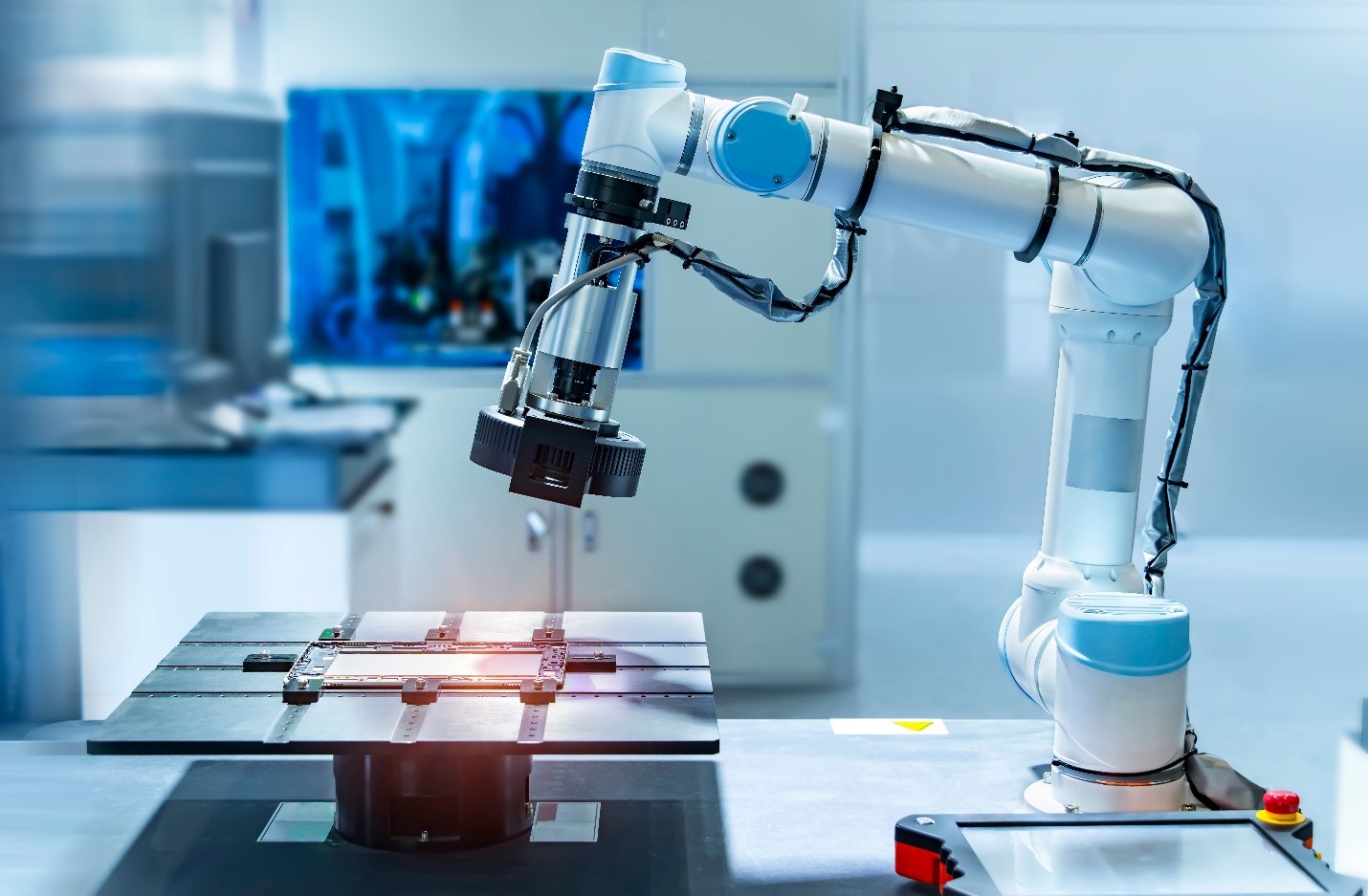
Examples of applications for industrial collaborative robots (Cobots)
Collaborative robots, or cobots, are revolutionizing the industrial landscape. Designed to work alongside human workers, these robots enhance productivity and can help address labor shortages. Their capabilities will make them essential in many sectors, including assembly, packaging, quality control, and more. Explore some applications and see how they can be integrated into your work environments.
Read More
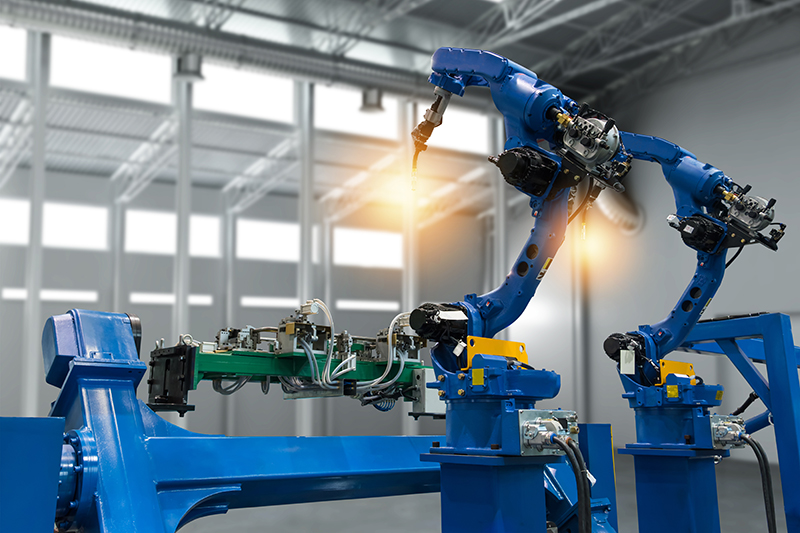
The 6 main reasons to integrate an industrial robot
Are you looking for an innovative and efficient solution to increase your productivity, reduce your costs, and improve the quality of your products? A robotic cell tailored to your needs is the solution.
Read More
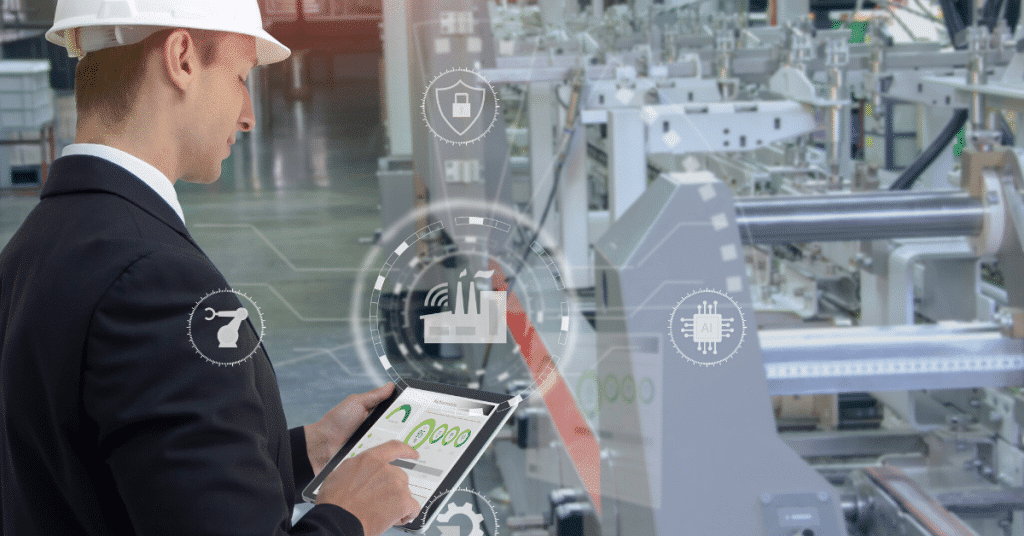
MLX300 – A 3rd generation, more innovative than ever!
The MLX300 is Yaskawa’s third-generation solution for environments requiring robots to integrate with programmable logic controllers (PLCs). MLX300 is a software solution based on our advanced robot controllers, where all programming, configuration, maintenance and troubleshooting are done through the PLC interface via additional instructions (AOI).
Read More
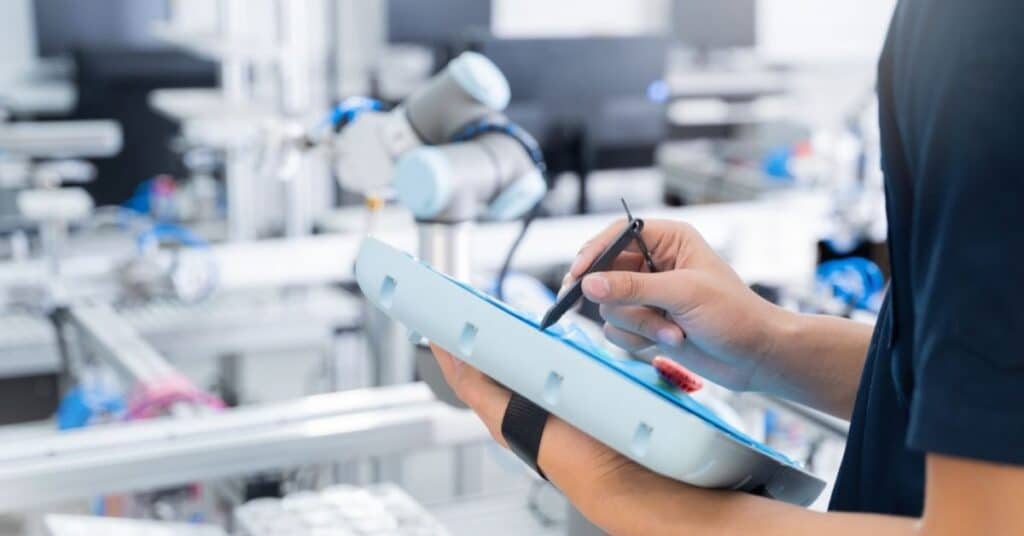
Robotics: A powerful partner during Covid-19
With factory closings, shortages, delivery disruptions, and a paralyzed supply chain, the pandemic that has turned the world upside down is more than ever highlighting the pressure that the world economy is putting on manufacturing production. A host of factories are now turning to traditional and collaborative robotics in order to overcome the major challenges raised by COVID-19. In the age of the coronavirus, how can industrial robotics benefit your plant?
Read More